Improving building performance requires coordination among many different industry players. The Building Innovation Hub (Hub) in Washington DC is a project from IMT that helps the building industry do just that. Below is an interview that Hub staff conducted with DPR. The original post is on the Hub website.
The Hub loves getting to know our members. We recently chatted with Camilo Garcia, Washington DC-Baltimore Business Unit Leader and Chris Hoffman, Northeast Preconstruction Lead, about becoming an Innovator-Level Member of the Hub, and the biggest challenges and opportunities for the building industry.
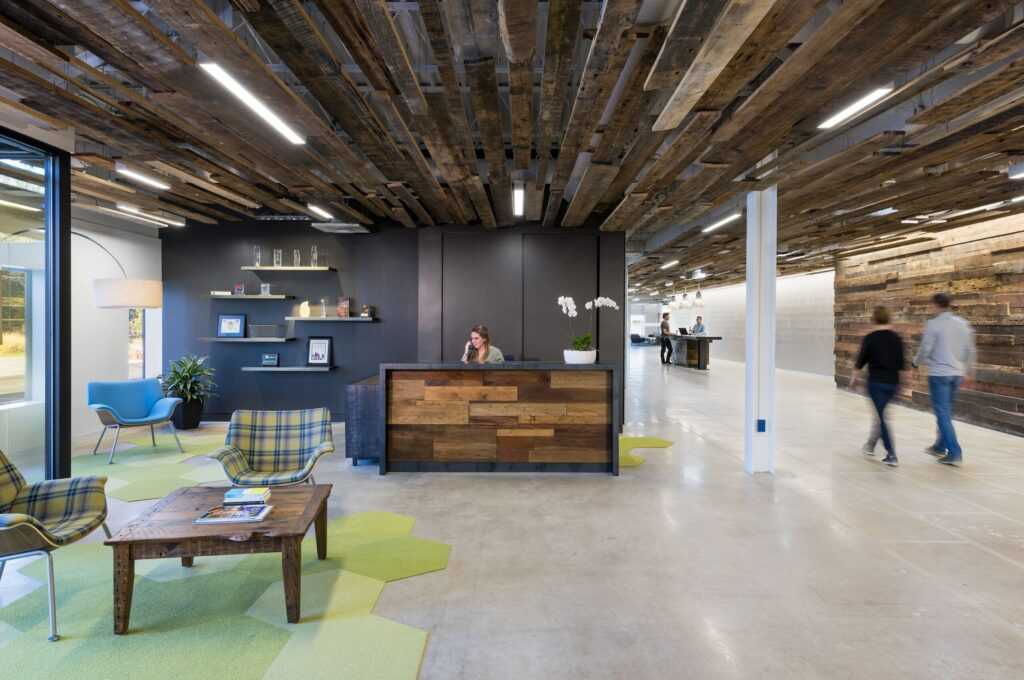
Why is building performance important to DPR right now?
Chris Hoffman: Two ways to look at it are as an employer and as a builder. From employer standpoint, we’re trying to be at the forefront of performance in terms of both energy efficiency and the health and wellbeing of our staff. We need to do that to retain the best talent and recruit new employees, given the high demand for talent in the sustainable building field. Our clients have the same needs. They want sustainable and healthy work environments to be able to recruit the best and brightest, and they want the long-term stability in their lower operating costs that high-performance buildings provide.
Camilo Garcia: We truly believe that this is the right thing to do from an environmental and social perspective, so we can make an impact on what’s happening in the world. We have our names on what we build and we want to walk the walk on this. Several of our offices are net zero certified and we use our own buildings as living laboratories to test out new high-performance building strategies. In our Reston office we have tried things—technologies, approaches, ideas—that are ahead of what’s being done elsewhere, such as installing a plug load reduction system that reduces phantom energy loads; SolaTubes as a part of our daylighting strategy; and a brightly colored, fully-displayed, highly-efficient mechanical system with a heat recovery chiller and dedicated outdoor air system (DOAS). Sometimes they work and sometimes we may need to spend more time getting them right, but it’s important that people see us taking action, because action speaks louder than words.
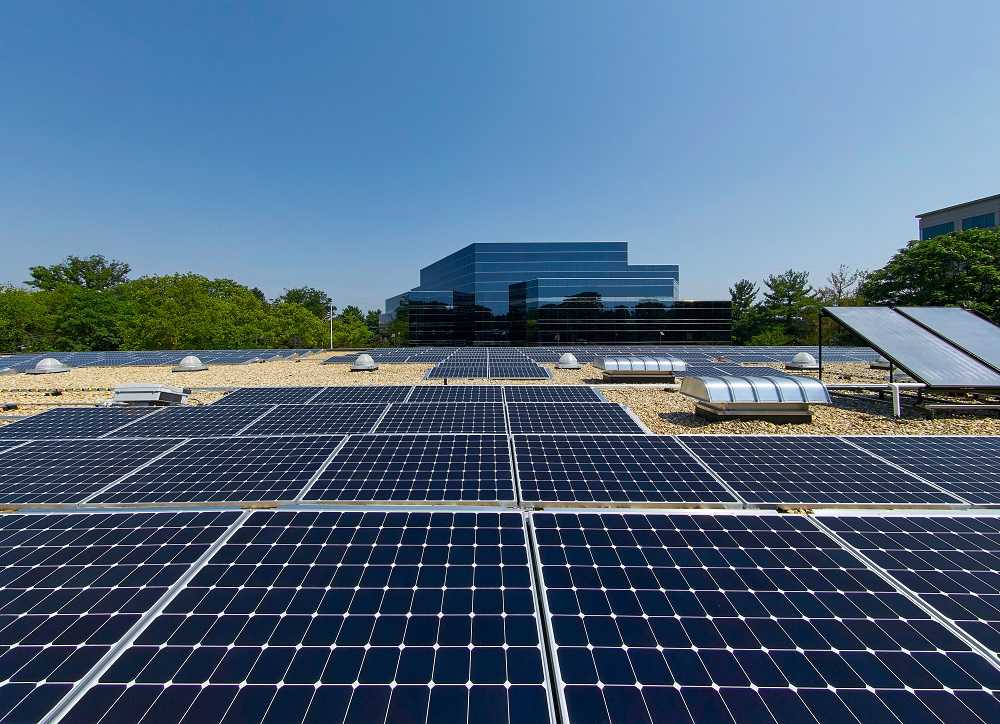
As demand for higher-performing buildings increases, what are the challenges and opportunities for the construction industry?
Garcia: The impact of this on our industry is huge. We need to look at the holistic lifecycle of a building to understand the impact—not just on individual people or occupants—but also on city-, infrastructure-, and the community. And unless and until we start willingly testing and trying to build with more efficient systems and strategies, we won’t be able to have the demand that will take the building industry to the next level. For example, I met with a client earlier today that committed to doing more mass timber. This willingness to prioritize cutting-edge, sustainable practices demonstrates leadership and will help propel the industry forward.
Hoffman: One big challenge, in terms of a holistic lifecycle approach, is to improve public and private partnerships. If we’ve got a client who’s trying to improve the energy efficiency of a building, how they can take advantage of the infrastructure surrounding their property. For example, how can the team use adjacent sanitary lines or metro exhaust for heat transfer? We need to leverage public-private relationships in new ways that eliminate red tape and allow us to collaborate as a whole city and a unified community to address the climate crisis in a unified way. Another challenge is really the unknown. We need to think creatively, but organizations don’t always want to take the living laboratory approach. We need to find a way to multiply those types of organizations and get them to work together to move the industry forward.
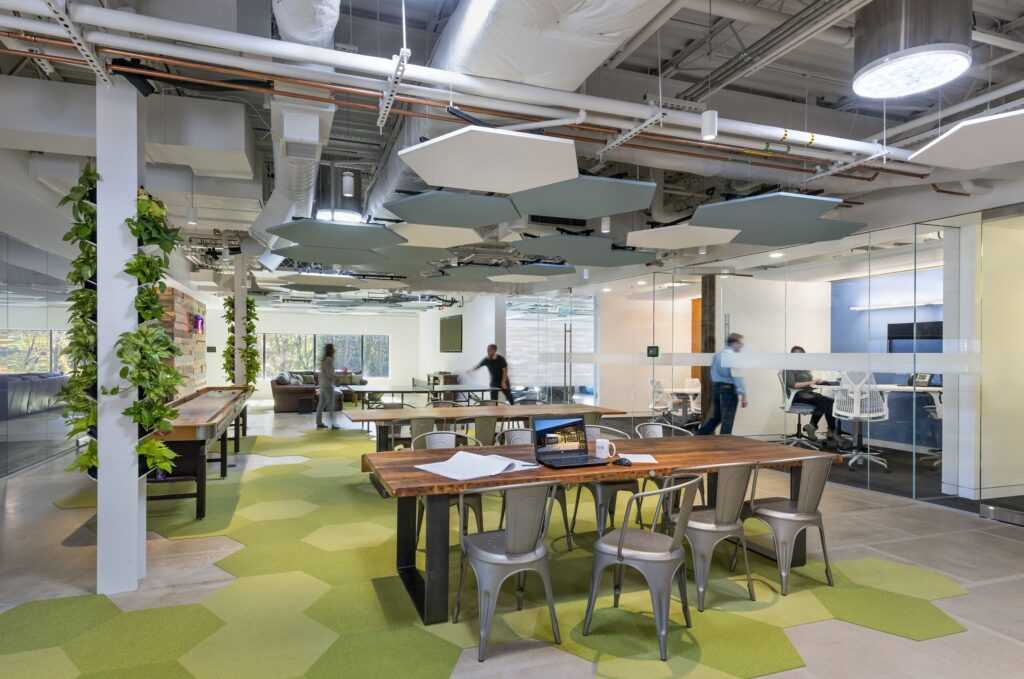
How is DPR looking to address workforce development challenges?
Garcia: This is a priority for us because as an industry, we have some big gaps. We are at an intersection of technology and craftsmanship. People who have been brought up through the trades have a different set of experiences and skills from newer people who are more experienced with technology. That can create tension between people who want to use the latest technology and people who want to get their hands dirty. We have to address this issue now, with schools, by looking ahead at least ten years to ensure we have people available with the right skills and experience to do the work we know will need to be done.
Hoffman: We need to make being a craftsperson an exciting opportunity, not a secondary choice because someone didn’t go to college. Folks earn a great living in this industry and create amazing buildings. We need to find a way to present that to middle and high schoolers, and to help them understand the connection between technology and craftsmanship. As a self-performing general contractor, DPR is developing our own talent in the trades to do our part in addressing workforce development challenges and creating career opportunities.
Garcia: DPR is a signatory to a union, which allows us to work closely with them on recruitment and to reduce the risk of less available skilled labor in the future. We are also doubling down on everything related to pre-fabrication because it is not only a balance of craftsmanship and technology, but it can be produced more safely, at a high-quality, and it allows the work to progress faster on job sites, which benefits our clients.
What are you most excited about accomplishing in partnership with the Building Innovation Hub?
Garcia: We are excited to lead the industry. We need partners to meet all the new DC regulations and also to be part of innovating and changing the market. The question for us is how can we support each other to maximize impact?
Hoffman: At DPR’s Core, we strive to change the world and respect the individual. We can change the world and make a better environment for our people by working with organizations like the Hub.
Garcia: General contractors are the ones putting environmental policy and client goals into practice every day. We are hands on, working on the front lines. That’s why we are always trying to educate our teams about what their work is accomplishing, and the larger goals it is helping to achieve. We see the day-to-day hurdles that get in the way of more sustainable buildings. Together, DPR and the Hub can establish a feedback loop on balancing the realities of the construction industry with the visionary solutions we need to all succeed.